在光学设计中,使用非球面可以简化光学系统的结构,减小透镜厚度,使实现更大的相对孔径成为可能。同时非球面的使用几乎可以矫正除色差之外的任意像差,可以说是光学设计的一大利器。 非球面技术发展初期,由于设计复杂,计算量大,加工检测也更困难,同期工艺水平难以达到设计的精度要求,就只能应用于一些像质不高的光学系统中。随着工业制造的不断发展,以及非球面加工与球面加工的成本越来越趋近于同一数量级,非球面的应用日益增加,不仅用于成像质量要求不高的系统,同时在照相摄影、广角、大相对孔径、变焦距等物镜中广泛使用。 通常在 Zemax 设计软件中使用最广泛的是 Even Asphere ( CV 里面是 Asphere ),此外还有 Q-con 非球面和 Extended Asphere 这两种常用面型。本次推文将以偶次非球面面型为例,尝试讲清楚非球面在制造之前,设计人员如何分析以及模拟面型误差,以便在图纸中准确表达对面型的要求。非球面透镜的传统定义如下方程所示(由表面矢高(sag)定义): A4、A6、A8...= 第4、6、8… 次非球面系数。
非球面在制造的时候通常需要在图纸中注明面型公差:PV(RT) & RMS(RA) 以及AS(亚斯)这三个比较重要的规格,更高要求的可以再加入 slope 公差要求。 如下是对应的计算公式: 
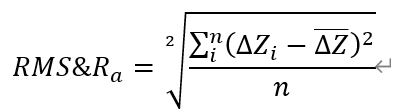
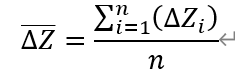
以 UA3P 测试机台为例,一般生产完成,供应商会给出如下非球面测试数据和曲线。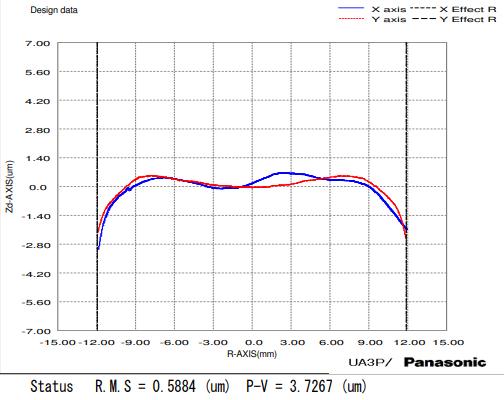
上图中的数据和曲线是通过实测面型数据和设计面型数据的差值得到,表明了目前加工完成面型的 RMS、PV 以及 AS 数据,同时也可以根据当前 PV 的形状,得到目前成型面型和设计面型的正负偏差(光学设计中,正负偏差对像质的影响也不同),方法如下:模拟之前需要有一个简单的概念,非球面的面型是通过上述公式,一个径向高度对应一个SAG,然后软件把足够多的SAG按照径向距离连成线,便构成了看到的非球面的轮廓。同时实际测量中也是这样,通过接触或者非接触的方式扫描出整个面型轮廓数据,然后与设计值进行做差,从而得到面型PV 数据,再把这些数据按照公式计算,得到 RMS 数据,最后形成了上面的测试图形。另外通过这些数据,也可以反向拟合出非球面系数,再回到设计软件,查看像质。
根据非球面公式和上述概念可以知道,对于一个给定的面型,想要让 PV 为5 μm,那就需要 SAG 变化5μm,根据非球面公式,当保证 C、K 不变,改变 A4、A6、A8……中任一系数,其他不动便可以实现。下图是按照公式,依次单独改变非球面高次项,形成的PV曲线。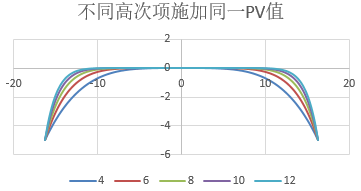
横轴为口径,纵轴为PV值
可以看到,项数越高,影响的面型 SAG 位置越靠近边缘。因此通过对各个系数同时改变,便可以模拟不同形状的PV曲线(U、n,W、M),再将这些系数代入软件中,查看对成像质量的影响。 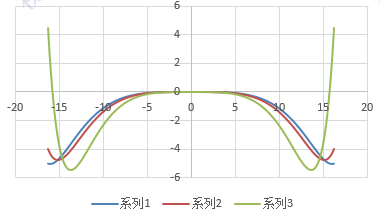
第二种方法 对设计SAG值随机施加扰动 上面一种办法通过公式计算,可以模拟出各种实际中会出现的曲线情况、PV和RMS所对应的系数,然后利用软件模拟系数变化来查看像质影响。第二种办法需要根据公式计算出设计值的SAG,然后直接施加一个随机数进去,如下图: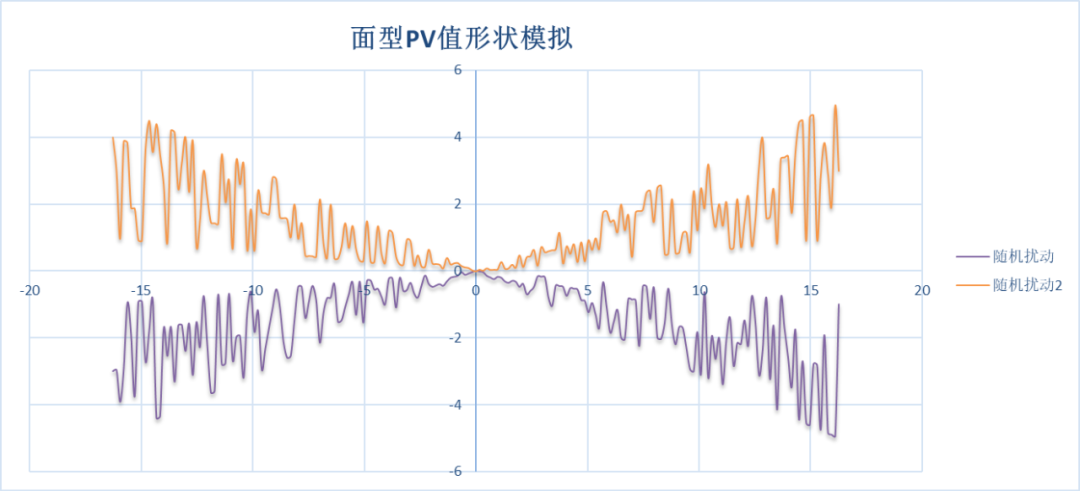
然后将扰动以后的 SAG 值,利用 Matlab 的拟合工具箱,利用自定义非球面拟合公式,拟合出高次项系数,代入软件中验证像质影响。 总结:两种办法都可以模拟实际生产中的测量数据,通过模拟得到的 PV 和 RMS 数据可以体现在图纸中去要求加工商。但是非球面系数本身并不具有实际公差意义,即无需在图纸中提系数公差!!!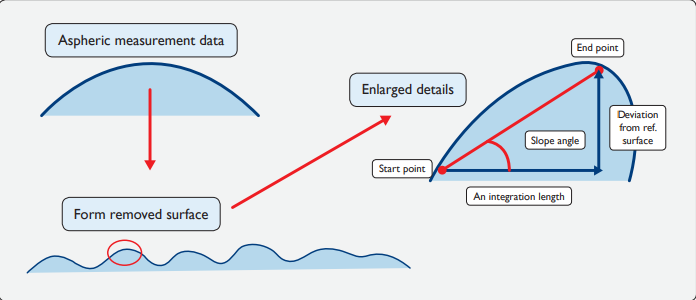
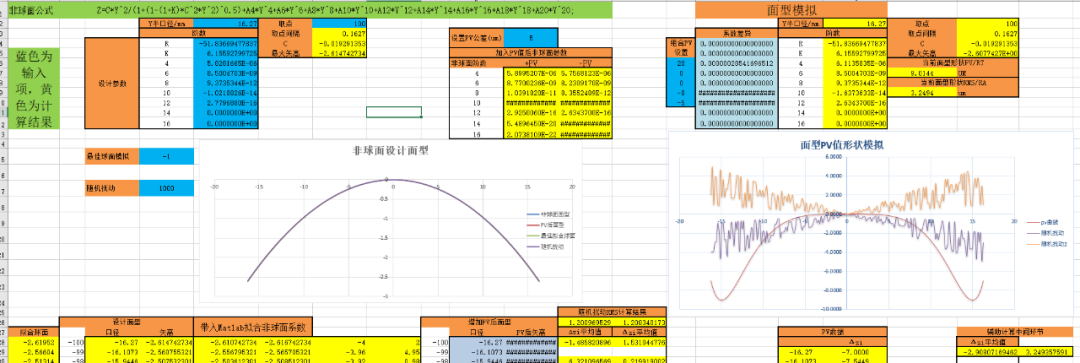
根据两种方法做的工具
|